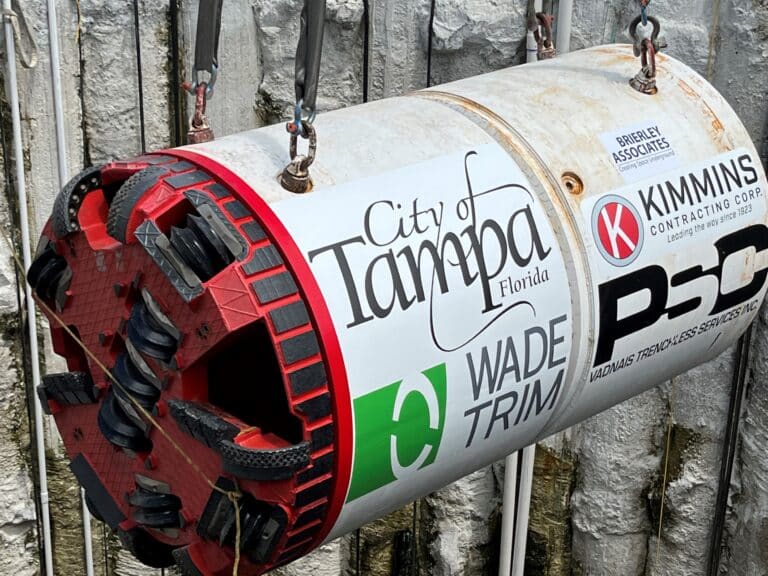
A new sanitary sewer forcemain is under construction to connect downtown Tampa to the existing wastewater treatment facility in the eastern Port of Tampa. Daily, more than 15 million gallons of wastewater, about 30 % of total flow, is conveyed by an existing forcemain which has exceeded its design life. The City of Tampa elected to deliver this project via a Progressive Design-Build approach. The selected general contractor was Kimmins Contracting Corporation of Tampa, and the designer was Wade Trim, whose local Tampa office is active in large diameter water conveyance throughout Florida. Brierley Associates was hired to provide specialty microtunneling consulting and construction supervision services. We assisted the D/B Team to prepare bid packages, led interviews with prospective microtunneling contractors, and prepared evaluations of the bids.
The subaqueous portion of the forcemain crossing over 3174 linear feet beneath the marine Ybor Turning Basin consists of a two-pass system of a 54-inch OD polymer carrier pipe installed within a 78-inch OD steel casing pipe between the Port of Tampa and Fort Brooke-Cotanchobee Park in downtown Tampa.
Challenging Site Geology
The project area is underlain by a mixed stratigraphy of geologically recent, poorly consolidated sediments overlying and intermixed with limestone bedrock. Dolostone layers and chert inclusions were commonly encountered especially within the westernmost portion of the crossing. The contact between the soils and limestone is irregular, with zones of rock dissolution and inclusions of chert nodules up to 2-ft in diameter. For the drive beneath the shipping channel with a dredged depth to a maximum of EL -42 ft, the microtunnel crown was maintained at El -54.5.
Extensive land reclamation in the early part of the 20th century dramatically impacted the shoreline in the project vicinity, which resulted in surficial fill sequences for both shaft excavations. A series of geotechnical borings were performed prior to construction both onshore and within the shipping channel to provide a geologic context and geotechnical parameters for tunneling design.
After interactive constructability reviews, a slurry TBM machine was utilized by the tunneling contractor, Primoris Service Corporation. Secant pile supported circular shafts constructed by Keller approximately 80-90 ft below ground surface provided watertight and safe ingress and egress for the MTBM and tunneling crews. The microtunnel was constructed using 78-in-OD, 1-inch wall thickness Tri-Loc steel casing pipe manufactured by Trinity Products. Six intermediate jacking stations (IJS) were installed within the casing pipe drive. Brierley personnel were onsite throughout the construction of the secant piles and during tunnel advancement, a period of approximately 26 months.
The challenges of advancing the microtunnel included minimal soil overburden, avoiding inadvertent returns into the channel, difficulty maintaining line-and-grade in the variable ground conditions, and spatial constraints for shafts and equipment laydown yards in this highly industrialized and urbanized area. Hurricane Ian gave a glancing blow to the worksite, requiring over a week of shutdown and restoration of the project works in the middle of tunneling activities.
The microtunnel was successfully advanced by proactive maintenance of all equipment during tunneling, continual assessment of actual geologic/geotechnical conditions in real time as compared to the design model, and careful survey control.
Among the lessons learned:
The Good: Primoris used an online data management program to allow the Project Team and City of Tampa to observe tunnel advancement in real time. The use of the program improved communication between the Microtunnel Contractor and the Project Team and reduced downtime due to uncertainties with tunnel progress and assessing line and grade relative to design.
The Bad: Tremie Seals were difficult to install and make watertight due to the presence of stiff to hard clays and high groundwater table.
The Ugly: The presence of sticky, limey clays encountered during mining was a constant challenge to maintaining slurry mud weights below 9 lbs./gal, which were considered optimal for transporting tunnel spoils through the slurry system. The issue was partially mitigated by using several polymer mud additives used to control mud viscosity and slurry velocity properties.
The image below, courtesy of MTS Tunneling Systems, illustrates the slurry conveyance microtunneling equipment used on this project.